The Influence of Bearing Selection on Gear Modifications
An important aspect of gearbox development is the practical design of gear modifications. The following article will demonstrate the degree to which the selection of rolling bearings can influence the required gear modifications, using system analysis from the FVA-Workbench.
Design of Gear Modifications
Load-induced deformations and displacements in gearboxes can lead to significant gear mesh misalignment. This can cause uneven load distribution across the face width and greatly reduce gearbox safety factors. To avoid this scenario, gear modifications must be designed to compensate for these deformations. This requires detailed analysis of all gear deformations. The single-stage gearbox in Figure 1 will provide an example of how strongly the selection of the bearing type, together with the axial bearing design and bearing clearance, can influence gear modifications.
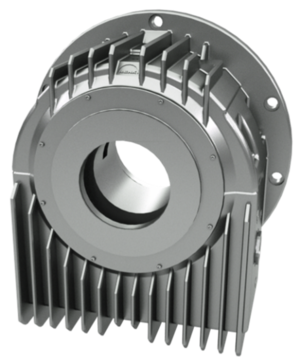
Calculation Example
The drive shaft of the gearbox is supported by two type 30324 tapered roller bearings in an X arrangement. The wheel shaft includes two type NJ 2230 cylindrical roller bearings in a floating arrangement. Figure 2 shows the bending lines of the two shafts.
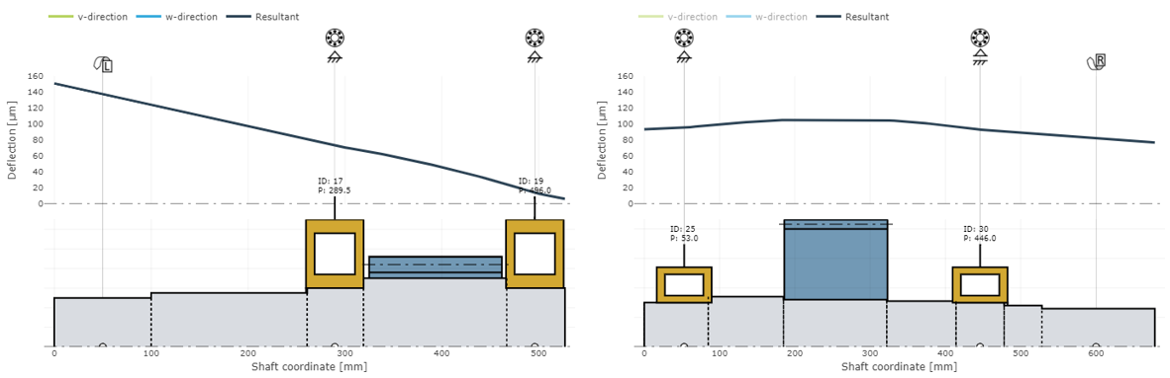
It can be seen that the deflection of both cylindrical roller bearings of the output shaft is nearly identical (Figure 2, right). In contrast, there is significant misalignment on the drive shaft. This is largely due to the so-called centering effect on the right tapered roller bearing. In the left bearing, only the rolling elements in the direction of the radial force are loaded (Figure 3, left), causing the bearing to deflect in this direction. In the right bearing, the restoring force on the shaft resulting from the radial force and the contact angle is lower than the applied axial force from the gearing. As a result, the shaft is pushed into the bearing so that the rolling bodies are in contact across the entire circumference (Figure 3, right). Thus, the shaft deflects only slightly in the direction of the radial force.
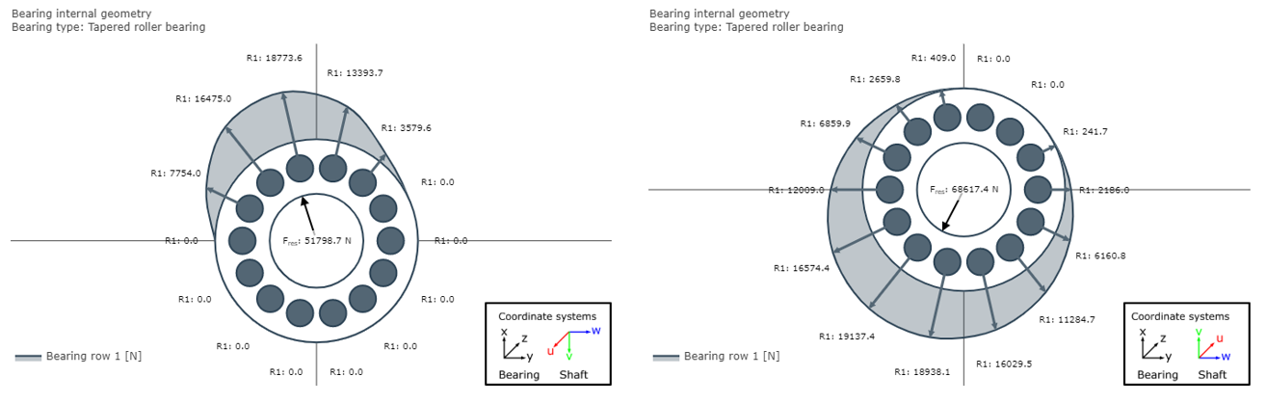
Figure 4 shows the load distribution across the face width, resulting mainly from the misalignment of the drive shaft, and the proposed modification for balanced load distribution determined using the FVA-Workbench.
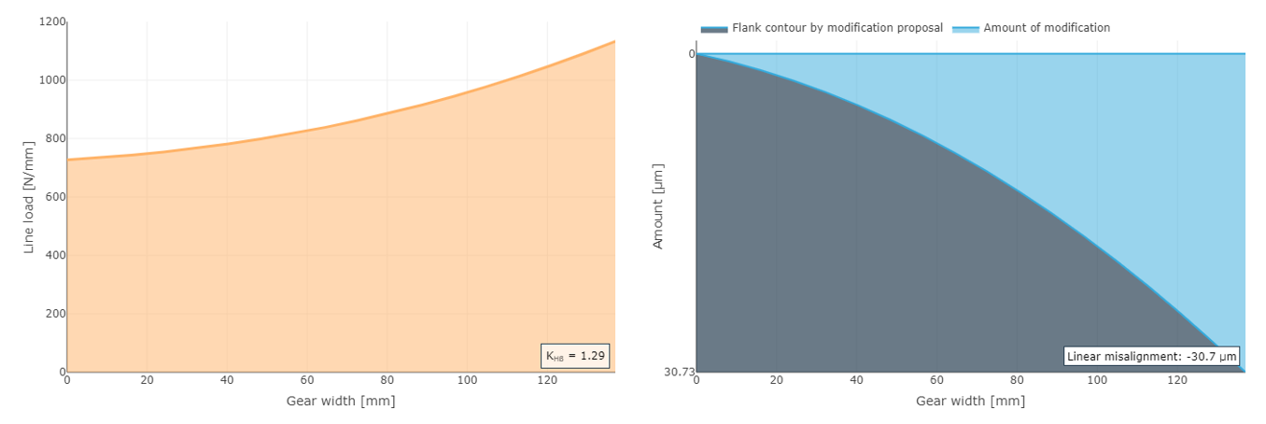
To counteract the centering effect described above, the right bearing can be replaced by a bearing with a larger contact angle, such as type 30224. This larger contact angle results in greater restoring force, which pushes the shaft away from the bearing center. Thus, the shaft lowers further, decreasing the misalignment and significantly reducing the amount of modification required (Figure 5).
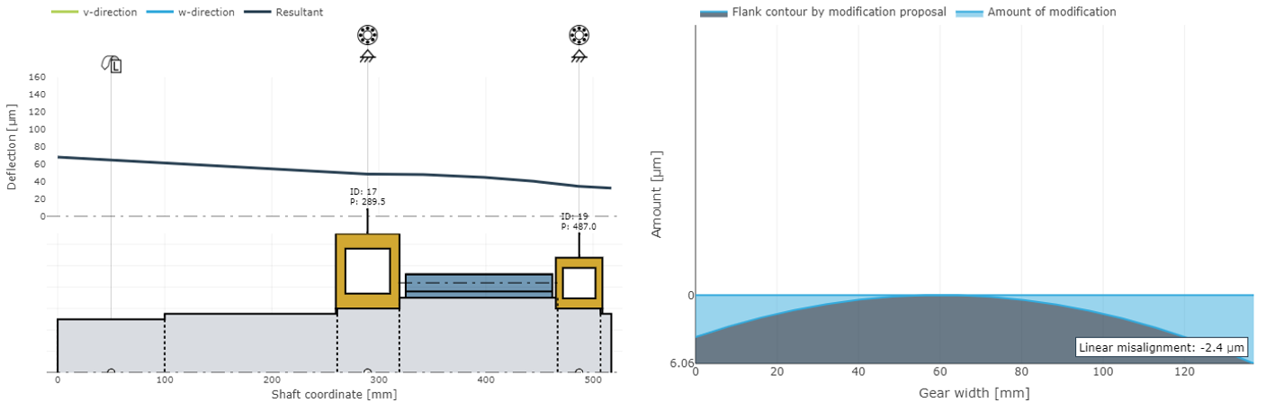
A comparable effect can be observed by selecting different bearings for the output shaft, such as replacing both cylindrical roller bearings with type 22230 spherical roller bearings (Figure 6), with a fixed bearing on the left and a floating bearing on the right.
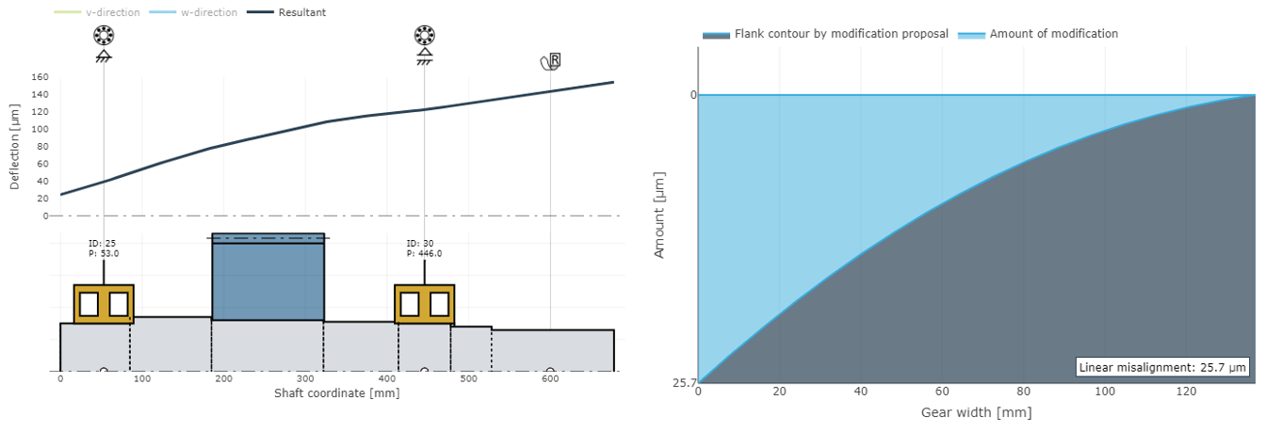
Here too, the shaft is centered on the left cylindrical roller bearing which, as a fixed bearing, absorbs the axial force. The preceding example clearly demonstrates the great influence of the bearing selection on the design of gear modifications. The centering of rolling bearings described above can occur with all bearing types that do not have a cylindrical running surface. The effect is increased with larger bearing clearances. The direction and position of forces can either increase or compensate for the resulting misalignment of the gearbox shafts in the gear mesh. Due to the large number of overlapping influences, consideration of all forces and deformations occurring in the transmission system, as offered by the FVA-Workbench, is required for the appropriate design of gear modifications. The FVA-Workbench can be used to determine the stiffness of a bearing arrangement as well as the associated lifetime and power loss.